
Colton Anderson
CUBESAT LAUNCHER
Our team of 4 had set forth to design and fabricate a 1U Cubesat Launcher for a company called Planetary Resources Inc (PRI). PRI had their own specific requirements for a Cubesat Launcher and wanted it to be much lighter than the other Cubesat Launchers on the market. I was in charge of designing some of the parts for the launcher but my largest contribution was the dynamic simulation in Matlab as well as machining the Cubesat Slider Plate on a CNC mill.
I solved the system of the door swinging open from 2 torsion springs as well as the Cubesat deploying from the compression spring. There were many different design variables all being an input into the system. The most important concerns were that the Cubesat would not hit the door during deployment and the Cubesat would eject at a certain velocity in a linear trajectory. By solving the differential equations and varying the design parameters I was able to choose a combination of torsion springs and a compression spring that would work with the assembly. High speed camera testing at 120 frames per second was done to verify that the springs had the optimal spring rate and preload in order for the Cubesat to not collide with the door. The dynamic simulation I worked on calculated the time it would take for the Cubesat to eject out of the launcher and by comparing it to the high speed footage the percent difference was 15%.
CAD

CAD model of our Senior design project, a 1U Cubesat launcher for host spacecraft.
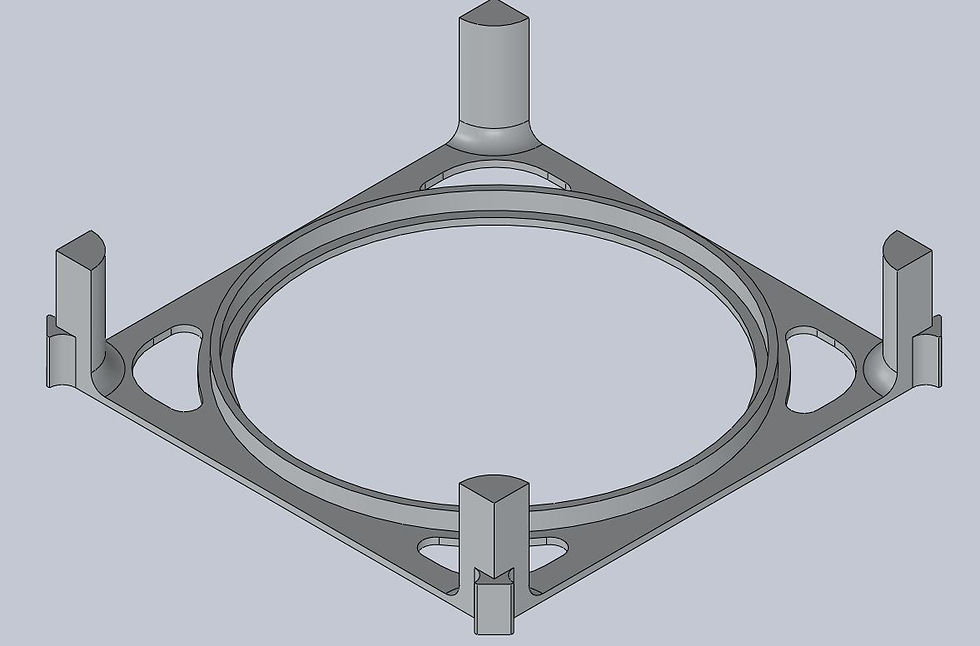
MACHINING

There were a few GD&T specifications that I checked on our Coordinate Measuring Machine (CMM).

Machining in pockets from back side because of the rigidity of the tool.
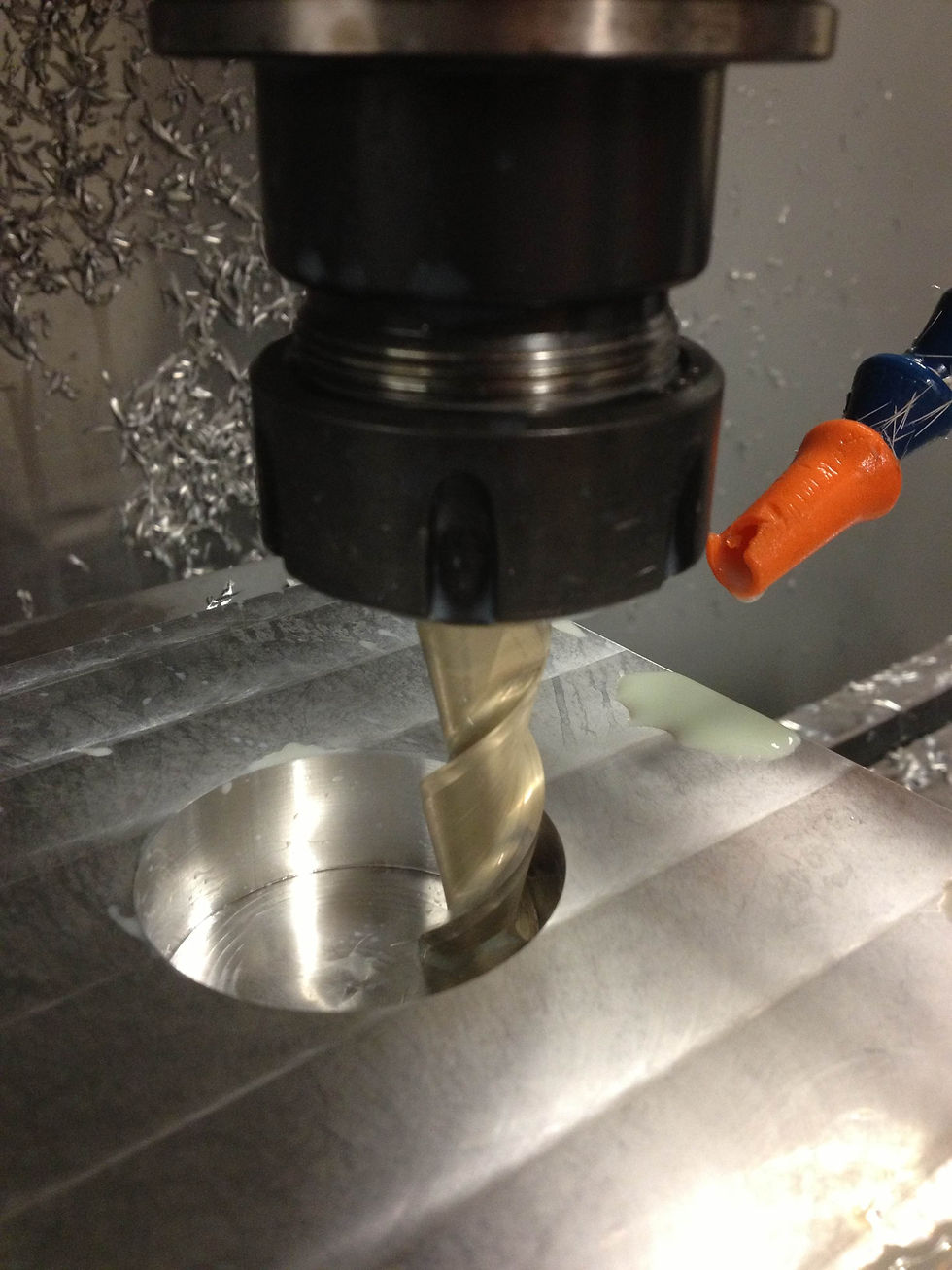
Experimenting with a "full" depth of cut and 0.06" step over with a not so rigid machine. Found the sweet spot after hand dialing in the feeds and speeds.
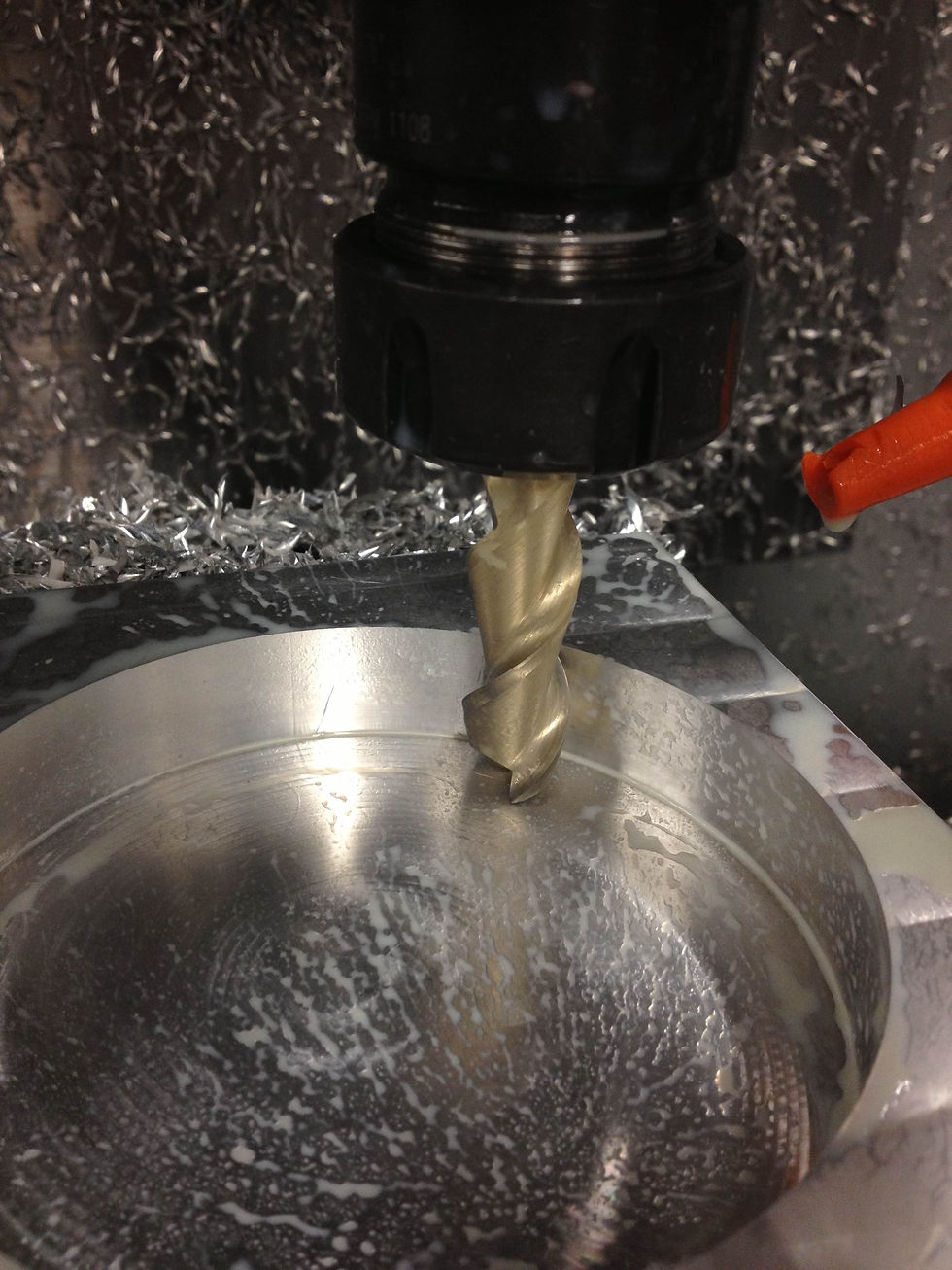
Pretty effective way of hogging material quickly.

Now ready to machine the outer profile

Machined inside circular pocket.
FINAL ASSEMBLY


Cubesat Launcher, Cubesat variable weight test dummy, and actual Cubesat. The launcher performed flawlessly every time and had a 15% difference between the actual ejection time and the dynamic calculations.