
Colton Anderson
​
FORMULA SAE
Results:
Formula SAE West (Lincoln, Nebraska)- 1st place overall in combustion competition and 2nd place overall in electric competition
Formula Student Germany (Hockenheim, Germany)- 7th place overall
I’m part of the University of Washington Formula Motorsports team where we design, manufacture, assemble, and test a formula style racecar every year. We have 70 extremely motivated students from all different majors around campus working on this project and we run it exactly like a business. There is a technical side as well as an administrative side which includes sponsorship, resource management, and public relations.
​
We go to SAE (Society of Automotive Engineers) competitions at the end of the build year in Nebraska, California, and Germany. Last year we took 4th overall with a 1st place finish in design in Lincoln Nebraska and 14th overall in Germany at the Hockenheim ring. The competition in Germany is the largest and most competitive in the world and all of the top teams attend. Our team has been running a combustion car for 24 years and this year we have decided to make an electric car since it will be the first year that Lincoln will offer the electric car competition.
​
My first year on the team (Team 22) I designed and manufactured the throttle body for the Engine team. My second year on the team (Team 23) I designed the Hub assembly for the Suspension team and this year (Team 24) I designed the Anti-Roll Bar assembly.
TEAM 24- SUSPENSION

Done on Solidworks


Finding the total deflection through the entire assembly using Linear solving methods for the purpose of time and multiple iterations.

Done on Solidworks


I had to add in splines in order to uniformly distribute the stress across the blade. This was also done in order to gain the most deflection at the rod end in the soft setting of roll resistance.
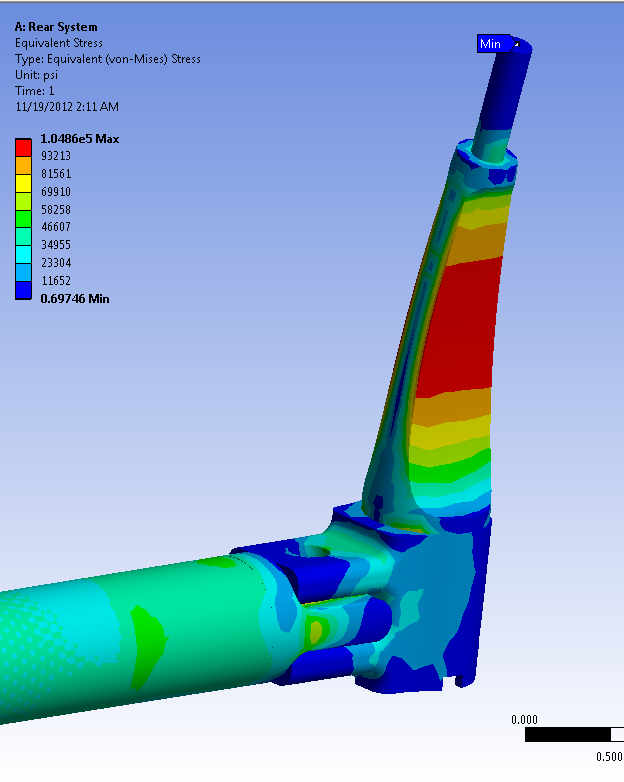
After 5 am the day before the design freeze a decision was made by me to make the blade out of Titanium Al4-V6. I was trying to achieve a large range of roll resistance and any combination of 4130 steel just wouldn't work in the analysis done on Ansys Workbench.


Ready to go on the car.
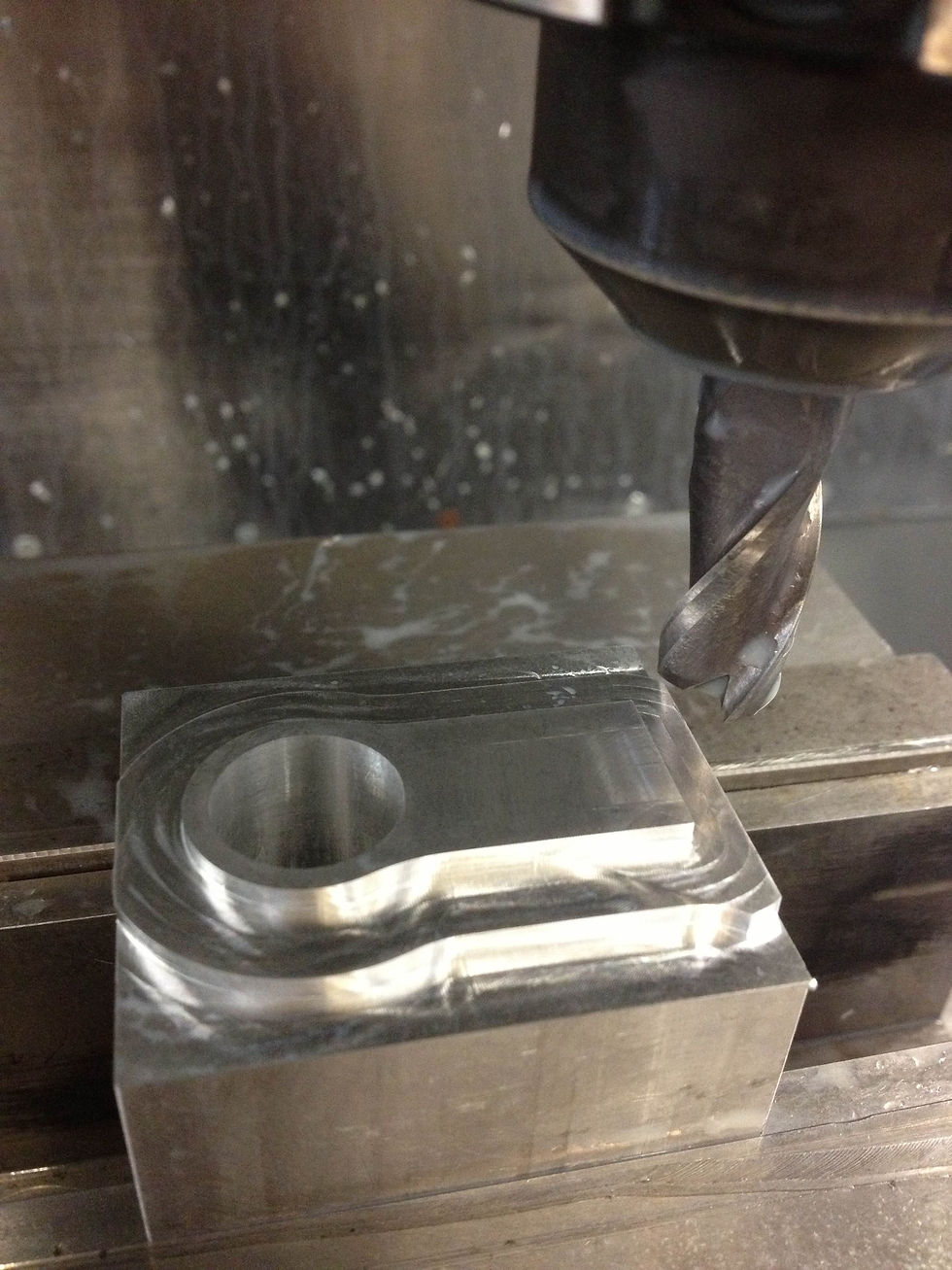
In the process of machining a 2D contour. Tolerances of plus or minus 0.001" met.

Using an 1/8" 3 Flute.
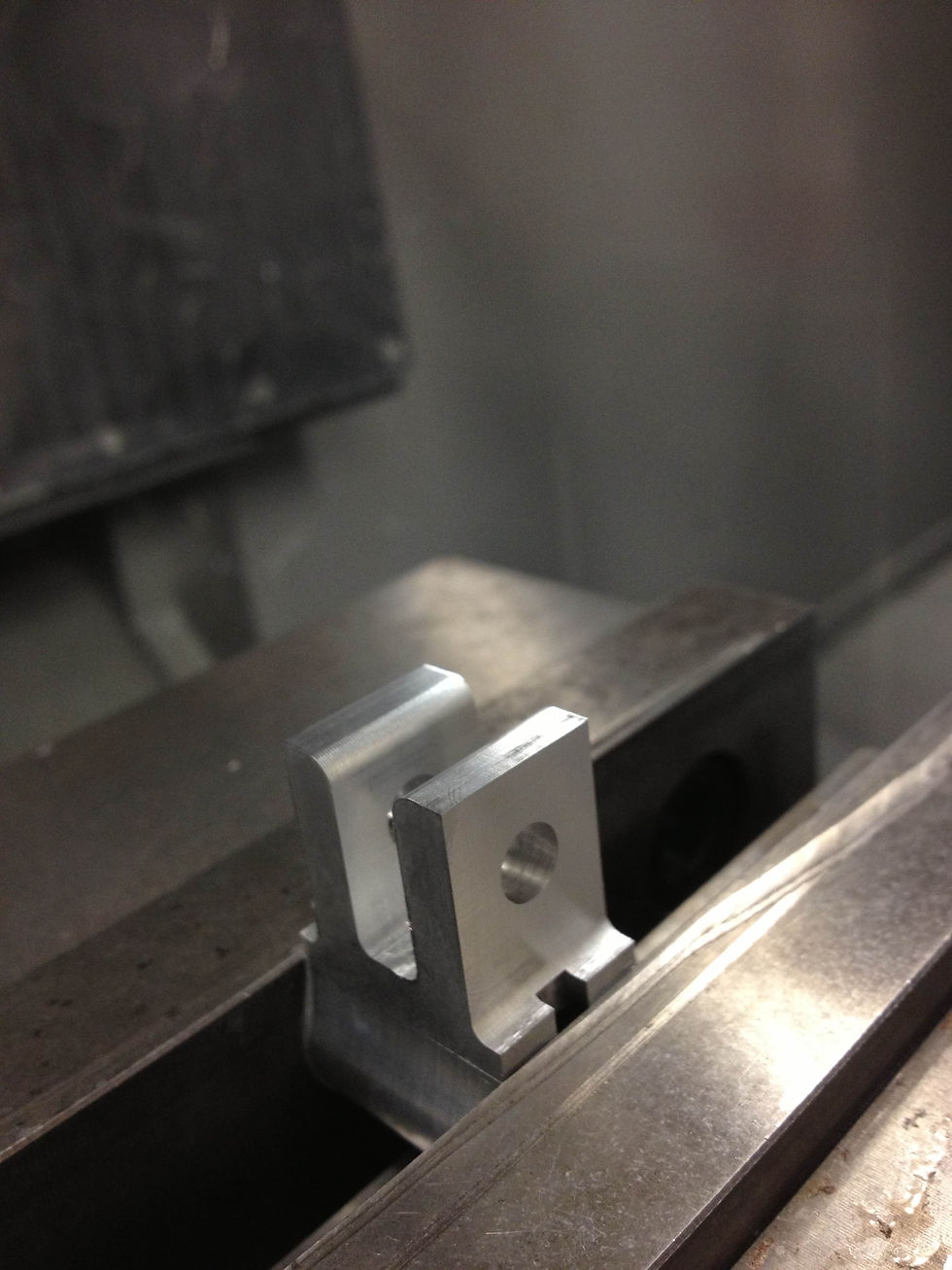
Machining tabs that will clamp the weld inserts attached to the torsion tubes. Using the "Parallel" feature in HSM works with a bullnose cutter
TEAM 23- sUSPENSION

Huge Design Change from past years. Centerlocking system was attempted 3 years before but not successful. Thin section angular contact bearings saved 2 lbs over the tapered rollers from the year before. Vernier scaled bearing preload feature on the inboard nuts since the bearings are extremely sensitive to preload. Integrated bearing preload and wheel speed sensor on the inboard nuts. I took on this challenge and every feature on the hub worked as planned!
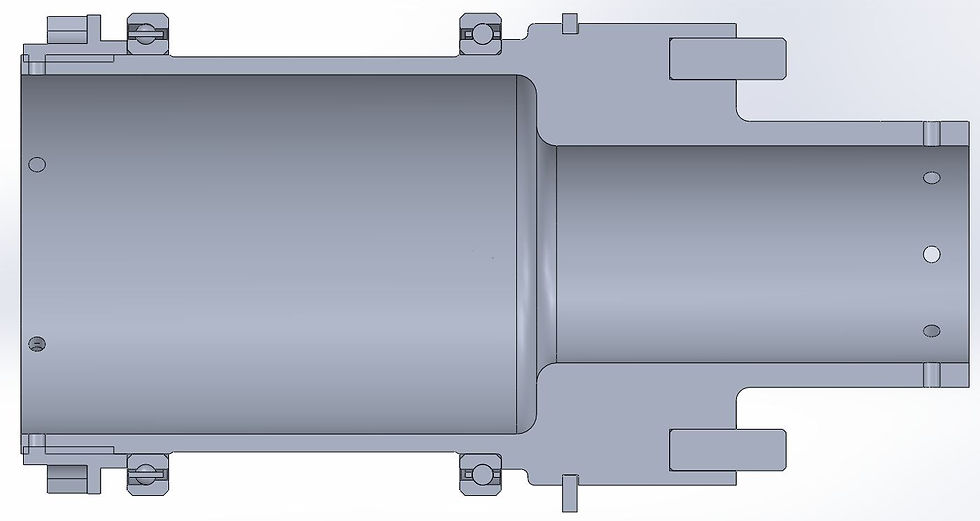

Huge design change- integrated CV joint eliminating the need for splining and saved 1 lb overall.

View of the integrated Constant velocity joint
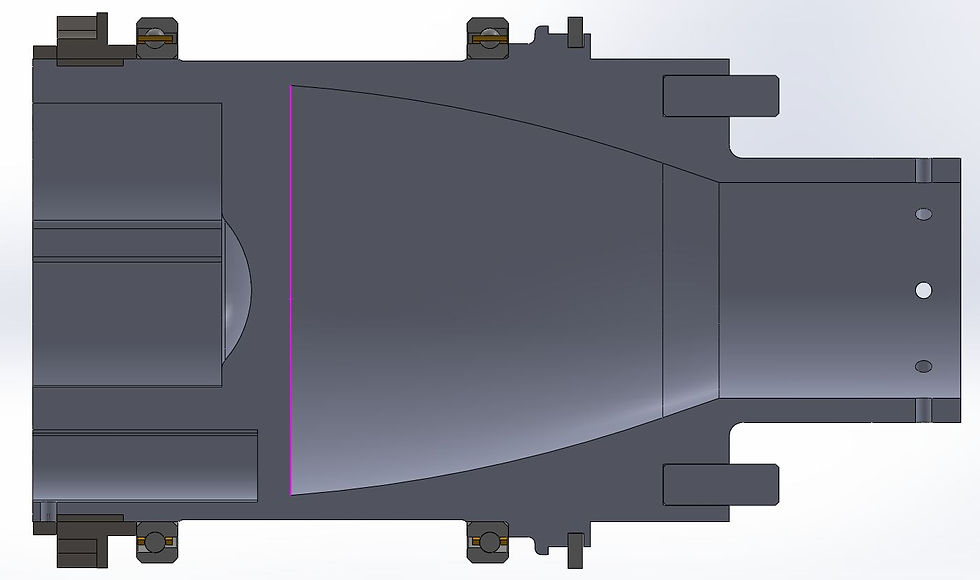

TEAM 22- ENGINE

This allows the butterfly plate to open linearly for optimal throttle response.
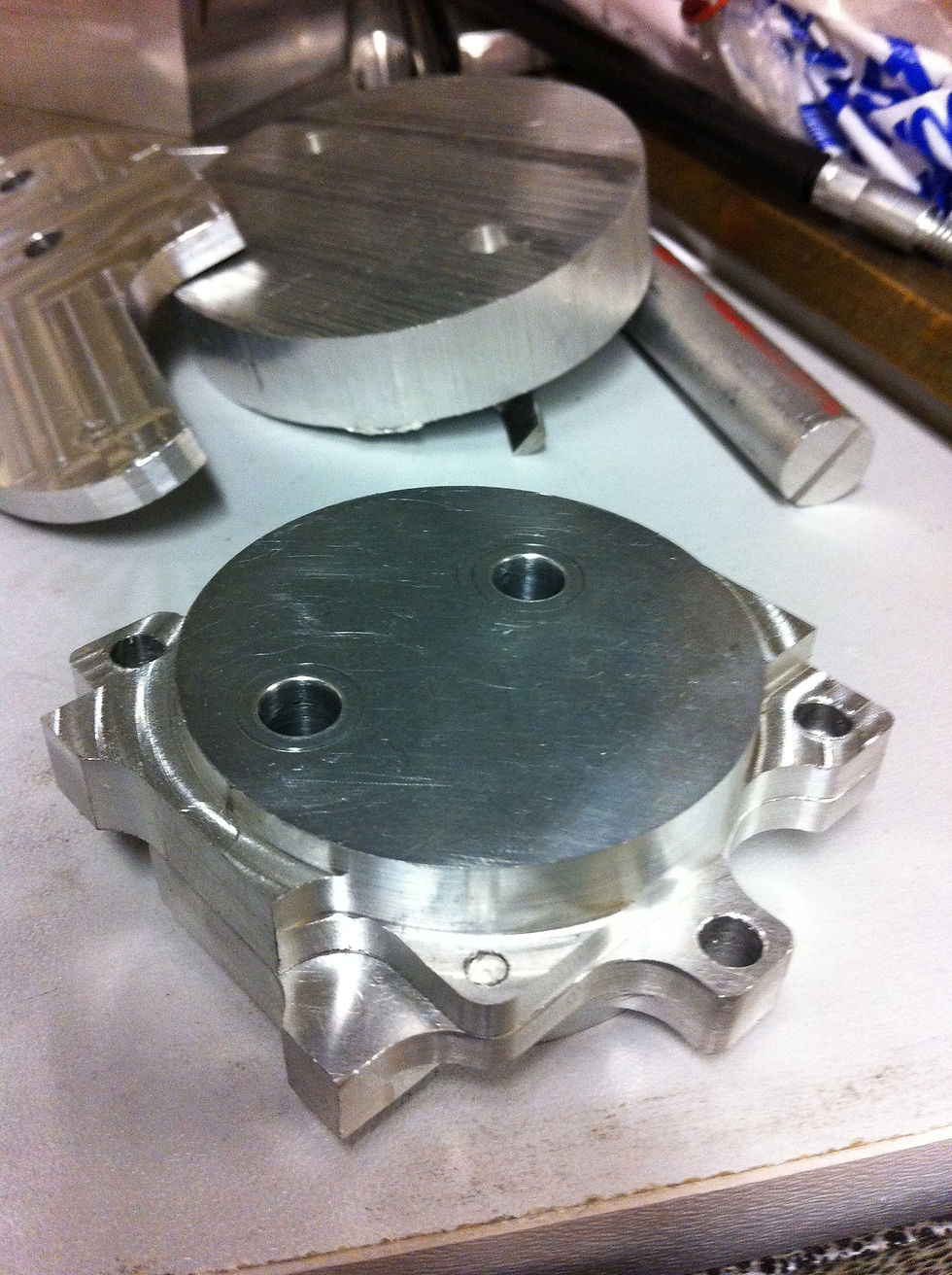
Multiple 2D profiles generated by Unigraphics NX CAM at different heights.
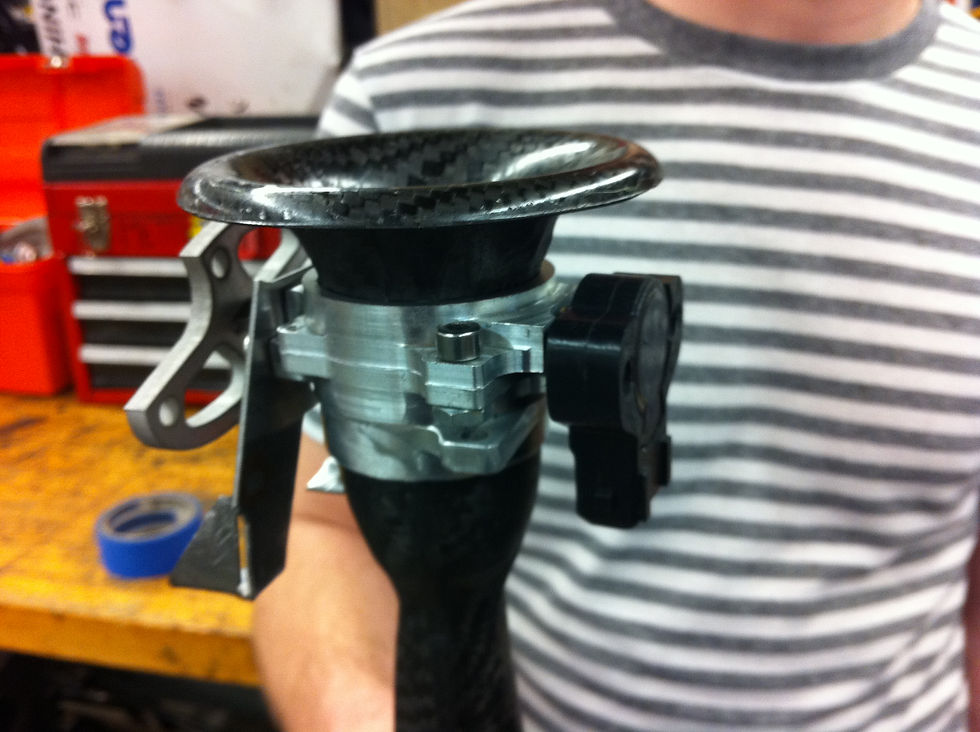
Materials used: Carbon Fiber, steel, aluminum, brass. Wet Layup was done on the bellmouth for increased flow.